European automotive manufacturers are under mounting pressure to meet accelerating market demands and compressed development cycles. While some competitors have nearly halved traditional timelines, many established OEMs still grapple with outdated workflows and process engineering bottlenecks. This case study explores how one leading European OEM cut equipment design time by 50% - from a 12-week standard down to just 6 - by modernizing its workflows and democratizing 3D modeling across the organization.
The Core Challenge
To boost cost efficiency and speed up production, the process engineering department undertook an in‐depth review of its processes, revealing significant bottlenecks. Although existing systems like CATIA are robust, their operation demands extensive expertise and continuous practice, requirements that many process specialists struggle to meet. The reliance on such specialized tools highlighted a broader obstacle: not all departments are equipped for intensive 3D modeling. Process specialists, who typically have the most direct insights into production challenges, were sidelined and their improvement ideas piled up, leaving urgent design needs unaddressed and contributing to an ever-growing backlog.
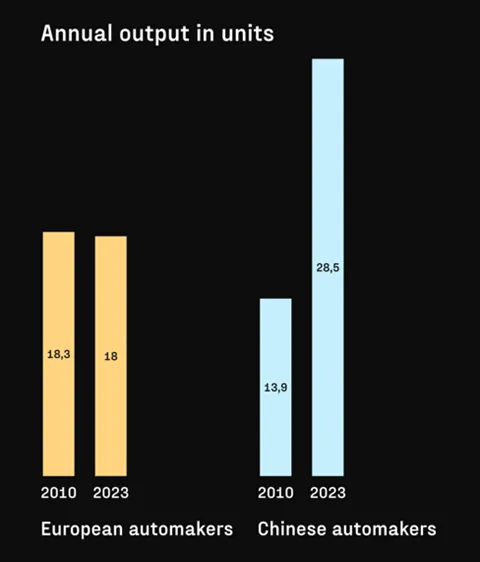
Other challenges that came to light include:
- Prolonged design cycles
Routine equipment design tasks took up to 12 weeks, delaying production improvements. - Limited access to specialized software
Only trained CAD experts could use the existing system, leaving process engineers dependent on overburdened design teams. - Lack of mobility
Desktop-based tools made real-time validation nearly impossible, as engineers on the shop floor had to request updates from distant CAD stations. - High licensing costs
Seats costing around €15,000 each restricted adoption to a small group, undercutting any chance of widespread improvements.
Looking for a better 3D design solution
Facing mounting project delays, the OEM assembled a cross-functional team to research more accessible 3D modeling options. They prioritized:
- Fast onboarding: So that process engineers, not just CAD specialists, could actively participate.
- Shorter design cycles: To move from a 12-week process to something leaner.
- Mobile compatibility: Allowing real-time review and edits on the shop floor.
- Cost-effectiveness: Reducing per-seat expenses to allow broader departmental use.
In pursuing a new solution, the OEM understood that it should aim to democratize 3D modeling, making advanced design capabilities accessible beyond the traditional circle of CAD experts.
Adopting a mobile-first tool
Through this evaluation, the OEM identified Shapr3D as the intuitive 3D design platform that would meet these requirements. Training, which used to span weeks, was cut down to days. Engineers quickly learned to create and modify 3D models themselves, accelerating feedback loops and reducing dependency on specialized CAD teams.
Key advantages
- Time savings: Design timelines dropped from 12 weeks to 6, speeding up production schedules and opening capacity for new improvement projects.
- Real-time validation: Mobile capabilities allowed process engineers to revise designs directly on the shop floor, shrinking feedback cycles from weeks to hours.
- Lower costs: Licensing decreased to around €1,500 per seat, roughly a tenth of the OEM’s previous spend. This enabled broader adoption across departments.
Results: Streamlined workflows and faster production
The switch to a more accessible, mobile-ready system had an immediate impact. Process engineers gained direct control over design tasks, freeing them to act on improvement ideas without going through multiple layers of approval.
- Eliminating bottlenecks
Faster design cycles drastically reduced the backlog of unimplemented optimizations. Tasks once stuck in the queue for weeks were tackled much sooner, keeping production lines flexible and responsive. - Cross-functional collaboration
Teams in logistics, prototyping and ergonomics, formerly siloed, could now share updated 3D models in real-time. Instead of waiting for CAD specialists, each group validated and adapted designs on the spot. - On-the-floor modifications
Engineers used tablets to refine equipment like trolleys or fixtures within hours of spotting issues rather than waiting weeks for revised CAD drawings.
This shift not only improved speed but also enhanced design quality by integrating frontline feedback at each stage.
Learn more about how cross-functional teams in manufacturing can speed up design validation with accessible XR-CAD.
What manufacturers can learn
- Make tools more accessible
When process engineers can handle their own 3D tasks, improvement cycles shorten. Entrusting the people closest to production challenges promotes faster, more accurate solutions. - Incorporate mobility
Real-time validation on the shop floor improves design accuracy and reduces waste. This also creates a more dynamic environment for continuous improvement. - Scale without overspending
Affordable licensing encourages organization-wide participation. More voices can propose, model and test ideas, leading to broader, more innovative outcomes.
From concept to execution
As development timelines contract across the automotive sector, rapid iteration and inclusive collaboration become critical. This European OEM’s experience shows that replacing legacy workflows with more flexible, user-friendly tools can cut equipment design time in half—and make continuous improvement an everyday reality.
By focusing on accessible software, faster iteration and real-time collaboration, manufacturers can equip their process teams to respond quickly to evolving production needs and stay competitive in a demanding industry climate.
This case study was sponsored by Shapr3D – the world’s most intuitive, mobile-friendly 3D CAD solution.